Industrial Pallet Racking: Custom vs Modular Solutions
Pallet Racking, Racking Inspections, Racking Repairs
The decision between custom-built and modular industrial shelving systems represents a significant investment that impacts operational efficiency for years to come. This comprehensive guide explores how facility managers can navigate this crucial choice to optimise both immediate functionality and long-term return on investment.
Understanding the Core Differences
Before examining specific advantages, it’s essential to clarify what distinguishes these two approaches to industrial heavy duty shelving:
Modular industrial shelving comprises standardised components engineered to function together in various arrangements. These systems function like industrial-strength building blocks—featuring pre-fabricated uprights, beams, decking, and accessories that can be assembled in multiple configurations to create versatile storage solutions.
Custom industrial shelving, by contrast, is designed and manufactured explicitly for your unique requirements. These bespoke systems are engineered from the ground up with your particular inventory profiles, operational workflows, and facility constraints in mind.
When Modular Systems Offer Optimal Value
Managing Budget Constraints with Immediate Needs
Modular heavy duty shelving typically requires a lower initial capital investment. Since manufacturers produce these components at scale, they benefit from production economies that translate directly to cost savings. For facilities operating with tight capital expenditure budgets, modular systems provide a practical entry point without compromising on essential quality standards.
Addressing Timeline Pressures
When facing tight implementation deadlines, modular systems present a clear advantage. Because components are pre-manufactured and maintained in suppliers’ inventory, delivery and installation timeframes are substantially reduced—often requiring weeks rather than the months typically needed for custom solutions.
Accommodating Evolving Storage Requirements
The defining strength of modular industrial shelving lies in its adaptability. For businesses experiencing seasonal inventory fluctuations or anticipating significant changes in storage requirements over the near term, modular systems enable reconfiguration, expansion, or relocation with relative ease and minimal disruption.
One distribution centre manager shared: “We reconfigure our modular shelving twice annually to accommodate seasonal product lines—an approach that would be prohibitively expensive with custom installations.”
Supporting Standard Inventory Profiles
Facilities primarily storing uniform items—standard pallets, consistent packaging dimensions, or regularly shaped merchandise—often find the standardised dimensions of modular industrial shelving perfectly adequate without requiring extensive customisation.
When Custom Solutions Deliver Superior Results
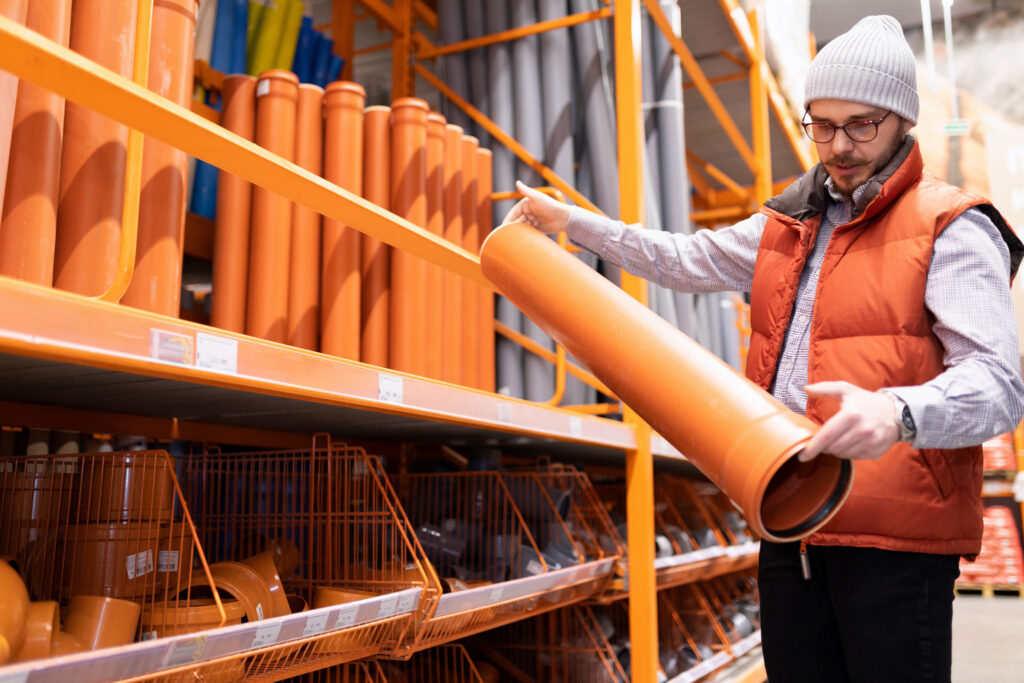
Maximising Challenging Spaces
Facilities with unusual architectural characteristics—restricted ceiling heights, irregular column placement, non-standard floor plans, or specific building code requirements—benefit significantly from custom heavy duty shelving that maximises every available cubic foot of storage capacity.
Custom solutions transform challenging spaces that might remain underutilised with standard shelving configurations. In one compelling example, an automotive parts warehouse increased storage capacity by 35% through implementing custom shelving designed specifically to integrate around structural columns and HVAC infrastructure.
Addressing Specialised Inventory Requirements
When inventory includes items with non-standard dimensions, unconventional weights, or special handling considerations, custom industrial shelving provides purpose-built solutions. Industries that particularly benefit include:
- Aerospace, with irregularly shaped components
- Automotive, with heavy and awkwardly-proportioned parts
- Electronics manufacturing, with sensitive components requiring specialised storage conditions
- Textile industry, with rolls of varying lengths and diameters
Optimising Operational Workflows
Custom industrial heavy duty shelving can be designed to complement specific operational workflows. Through detailed analysis of picking patterns, order fulfilment processes, and material handling equipment, custom solutions can reduce travel time, minimise handling requirements, and increase throughput in ways standard shelving configurations might not achieve.
A pharmaceutical distribution centre reduced order fulfilment time by 22% after implementing a custom shelving system designed specifically around their particular picking patterns and inventory rotation requirements.
Supporting Long-Term, Stable Storage Requirements
For operations where storage requirements are unlikely to change significantly over 7-10 years, the initial investment in custom industrial shelving often delivers superior long-term value through increased efficiency, higher storage density, and reduced maintenance costs over the system’s operational lifespan.
Conducting a Comprehensive ROI Analysis
The decision between custom and modular industrial heavy duty shelving ultimately depends on a thorough return on investment analysis. Consider these factors when calculating ROI for your facility:
For Modular Systems:
- Initial Investment: Generally 30-40% lower than custom alternatives
- Installation Timeline and Cost: Typically faster implementation with reduced expenses
- Storage Efficiency: Usually achieves 70-85% of the theoretical maximum for available space
- Operational Efficiency: Requires adaptation of workflows to standard configurations
- Maintenance and Modification Costs: Lower per incident but potentially more frequent
- Expected Depreciation Period: Typically 7-10 years
For Custom Systems:
- Initial Investment: Higher upfront expenditure
- Installation Timeline and Cost: More extensive planning and installation requirements
- Storage Efficiency: Can achieve 90-95% of theoretical maximum for available space
- Operational Efficiency: Optimised specifically for your established workflows
- Maintenance and Modification Costs: Higher per change but typically less frequent
- Expected Depreciation Period: Often 10-15 years or longer
Embracing a Strategic Hybrid Approach
Many facilities achieve optimal results through a strategic hybrid approach that combines the advantages of both systems. This involves implementing custom industrial shelving for areas with specific requirements or constraints, while deploying modular systems in more standardised spaces.
For instance, a food processing warehouse might utilise custom heavy duty shelving near production areas to accommodate unique container dimensions and high-volume movement, while employing modular systems in general distribution areas where standard pallets predominate.
Essential Decision Framework
When evaluating industrial pallet racking options, consider these five fundamental questions:
- What is your operational time horizon? Shorter timelines (under 5 years) often favour modular systems, while longer operational plans may justify custom investments.
- How specialised are your storage requirements? The more unique your inventory profiles or workflows, the greater the potential benefit from customisation.
- What growth trajectory do you anticipate? Rapidly evolving businesses may benefit from the flexibility of modular industrial shelving, while stable operations can maximise efficiency with custom solutions.
- What spatial constraints must you address? Unusual or highly restricted spaces derive greater value from custom solutions that utilise every available dimension.
- How is your budget structured? Operations with limited capital expenditure but more flexible operational budgets may find modular systems better aligned with financial constraints.
Implementation Considerations for Success
Regardless of which direction you choose, successful implementation depends on comprehensive planning:
- Engage stakeholders from operations, maintenance, and finance in the decision process
- Consider future expansion requirements, even if they seem distant
- Factor installation disruption into ongoing operations planning
- Evaluate compatibility with existing material handling equipment
- Assess long-term maintenance requirements and associated costs
No One-Size-Fits-All Answer
The choice between custom and modular industrial heavy duty shelving isn’t about identifying a universal “best” option—it’s about determining the right solution for your specific facility, inventory profile, operational requirements, and business objectives.
By meticulously analysing your requirements through the lenses of space utilisation, operational efficiency, implementation timeline, budget constraints, and long-term flexibility, you can make an informed decision that optimises both immediate functionality and enduring return on investment.
This significant infrastructure investment will impact your daily operations for years to come. Taking time to thoroughly evaluate both industrial pallet racking options—potentially with guidance from an experienced storage consultant—will yield substantial dividends in operational efficiency and cost savings throughout your industrial shelving system’s lifecycle.
For information on our shelving services or indeed other warehouse storage solutions, contact us here.